The fish feed must not only satisfy the nutritional requirements of the fish but its physical properties must be such that the feed can be used in modern fish culture systems.
Criteria for manufacturing pellets for aquaculture
During the manufacturing process, special attention is paid to:
– hardness of the pellet
– dust in the feed
– uniformity of size
– density
– that the feed is free of excess or seepage of oil
The objective is to produce a pellet of uniform size that is even, stable and dust-free. These properties are partially interrelated.
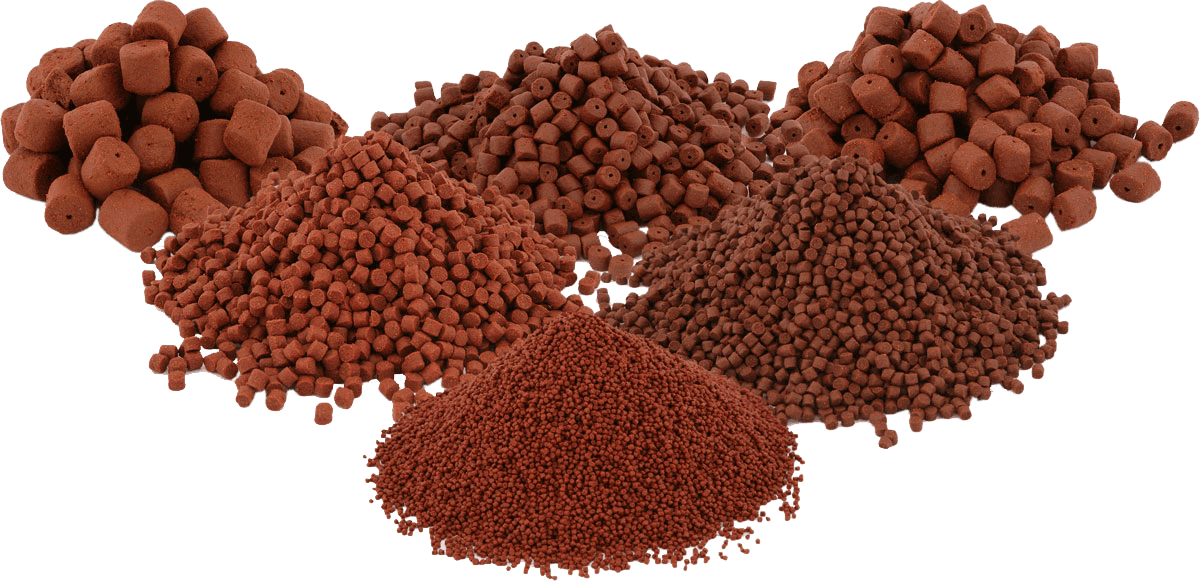
Food sizes are specified in great detail and carefully reviewed, both after extrusion and in packaging. The pellets must be free of any contamination, whether caused by food of different sizes or by physical objects.
Pellet powder origin
Dust in feed, from pellets that are broken or not adequately compressed in the manufacturing process, is generally a nutrient that fish lose and therefore an important element in costs.
In addition, dust is of course a nuisance as it disperses in storage warehouses or flies everywhere clogging equipment and tubes during feeding.
Therefore, special attention must be paid to controlling the level of dust and designing the food manufacturing process in such a way that dust is avoided first.
If the correct amount of adhesive material is added to the food (normally carbohydrates) and the extruder is operated correctly, an even pellet will be obtained, shiny on the surface, durable and resistant to breakage. The hardness of the pellets is checked regularly during the manufacturing process. Any dust level in the food is also checked regularly during packaging. A maximum dust level of 1% is considered normal.
Prevention and reduction of pellet dust during transportation and storage
Even if the feed leaves the factory in good condition and free of excess dust, the stability of the pellets may be affected by transportation and storage. Any moisture that penetrates the feed will soften the pellets and increase breakage and dust.
Therefore, the management of food in transportation, storage and distribution process is essential to avoid its increase.
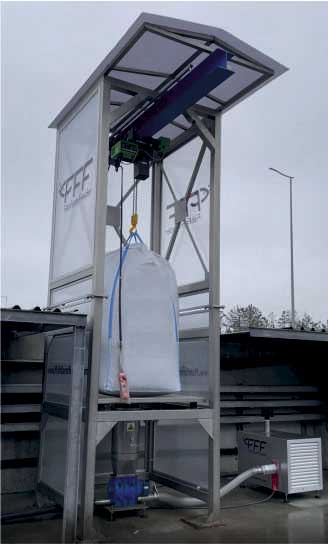
A good way to evaluate it is to sample the food just received in transport and measure the dust in a sample. With this information, monitoring must be done in the feeding system at the time of calibration and then when dosing it to the culture pond.
All feed systems will produce additional dust, the important thing is that it is not more than another 1%. Obviously, the initial integrity of the food will define the final result, so auditing this source of loss is essential as a practice in food quality control.
Mold risk control and oil filtration
Food showing mold growth should not be fed as it constitutes a health hazard. Therefore, you must pay close attention to the handling and storage of the feed and also that the equipment used (such as probes and dispersers) is appropriate to avoid unnecessary problems.
Modern foods contain a comparatively high level of fat. To retain fat in the pellet, optimal techniques are applied in terms of formulation, expansion and drying of the food.
Despite the highly developed techniques in this area, oil filtration problems can arise, causing oil to accumulate at the bottom of the bags or bins. This is due solely and exclusively to changing weather conditions, such as higher temperatures during the summer season. There may also be physical food pressure due to double stacking (i.e. two pallets or maxibags stacked on top of each other) over a period of time, which should be avoided. Be sure to store feed in a cool, dry place and ensure good stock rotation (first in, first out, within the limits).
Recommendations to maintain feed quality at aquaculture farms
In summary, fish feed manufacturing requires experienced attention to process parameters to ensure consistently good quality. The physical quality of the food can be affected by transportation to the cultivation center and by handling and storage at the center:
- Store feed in a cool, dry environment.
- Avoid double-stacking high-fat food.
- Keep stock levels low to ensure short storage times and fresh feed.
- Always keep samples, photos and control sheets to help solve any problems related to the physical quality of the food.
Review from EWOS/ Cargill good feed handling procedures.
Luis-Felipe Díaz is a veterinary doctor, specialist in aquaculture with more than thirty years of experience in team management and systems in aquaculture production, genetics, reproduction, production and processes of salmonids. Decades of experience dedicated to the design and operations of fish farms, RAS systems and sustainable processes in aquaculture. Since February 2024 Regional Director America at FFF.
Contact: Felipe.diaz (@) fishfarmfeeder.com
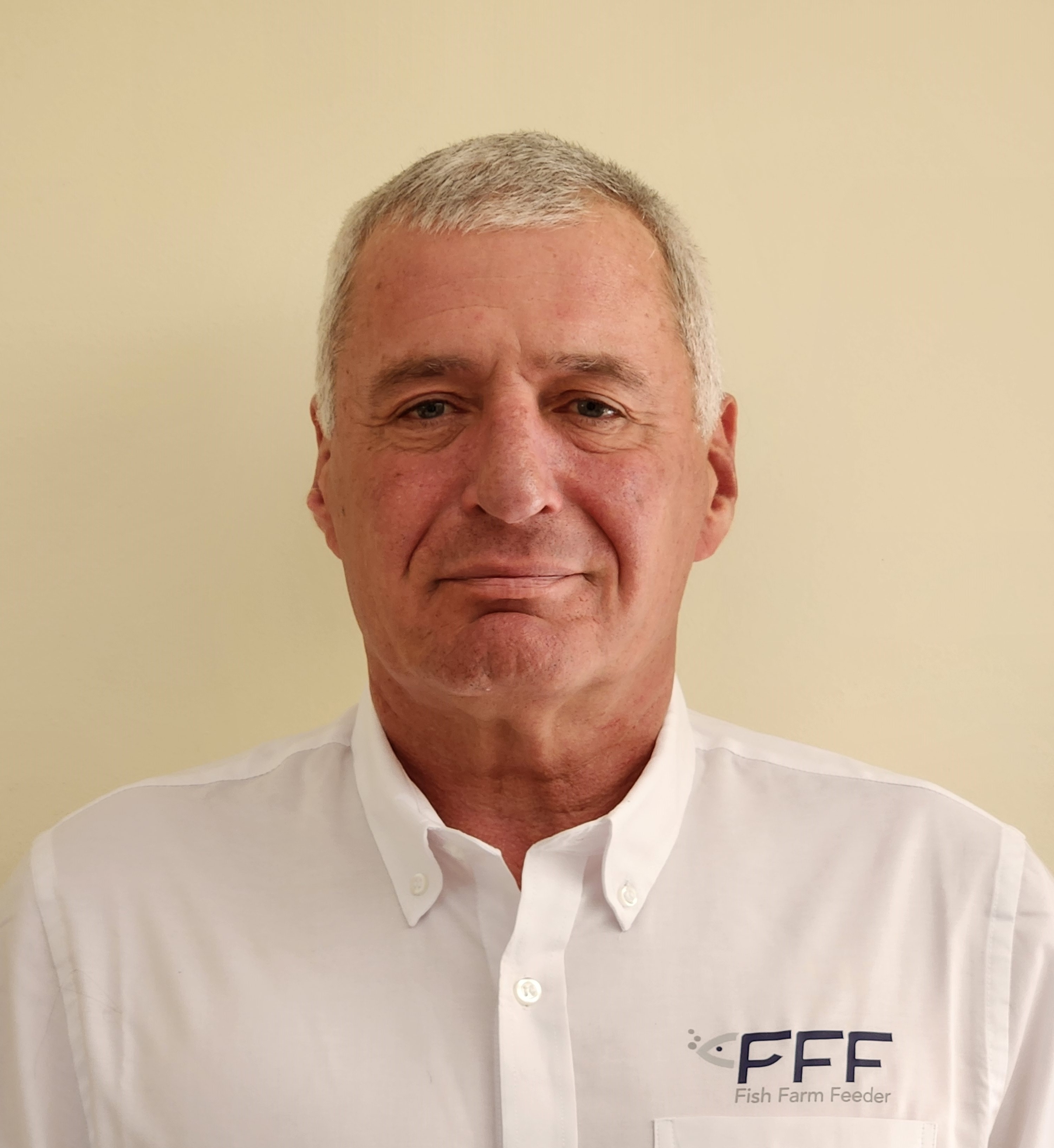